Our Yarn Dyeing Process: Solid Colors
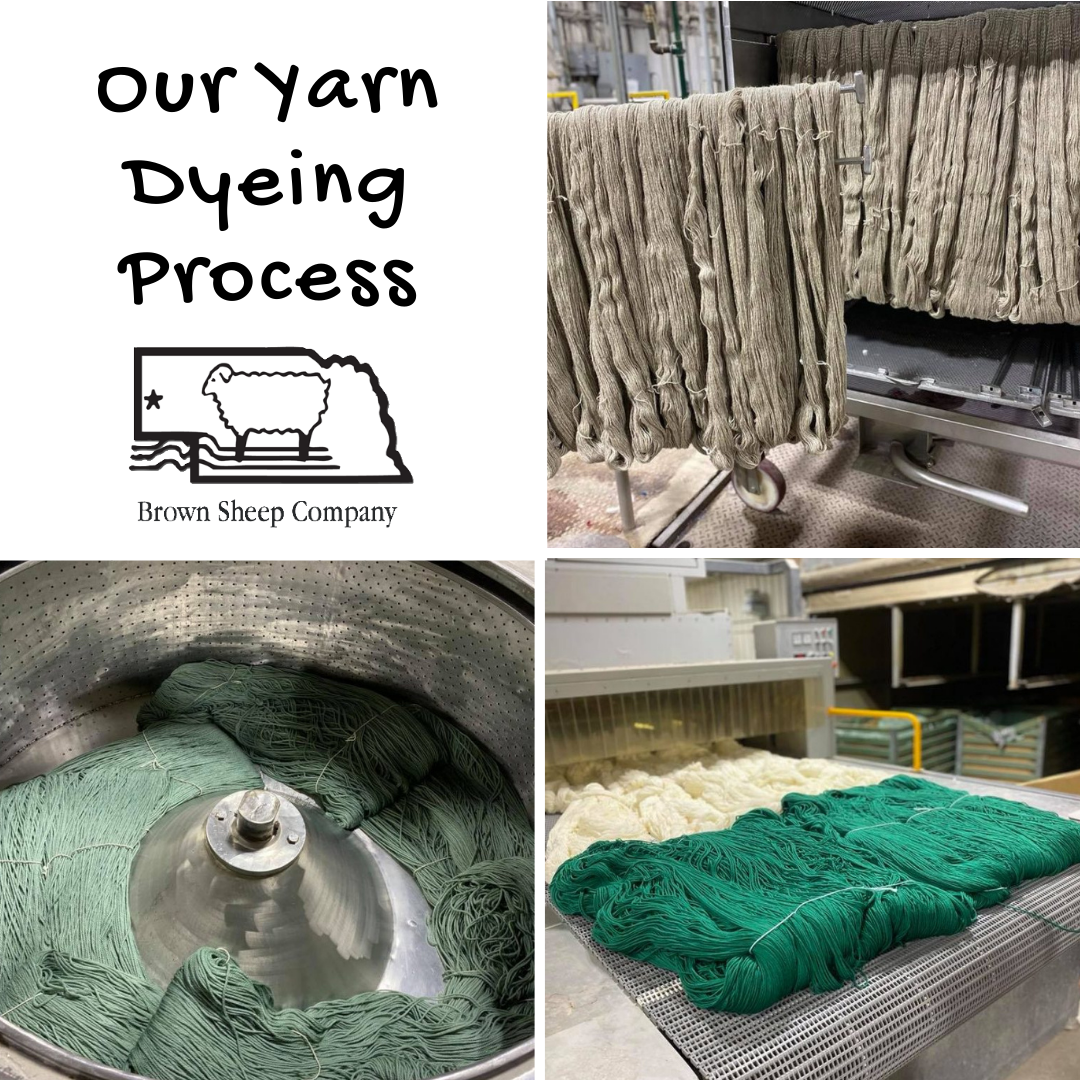
This month, we’re sharing a glimpse into the process of how we dye our yarns — specifically, our solid-colored yarns we dye in batches in our large dye vats. To learn about how our multi-colored yarns are dyed, see this previous blog post: A Sneak Peak Inside our Yarn Hand-Painting Process.
If you’ve had the opportunity to tour our mill, you’ve seen that we have divided our machinery into 3 main categories: spinning, dyeing, and packaging. Our dye department consists of 4 large dye vats, each with the capacity to dye a different size batch. Typically, a batch (or “dye lot”) is from 30 to 200 pounds of yarn. We usually dye the most popular colors—such as black, brown, and neutrals—in the largest quantities, with new or less popular colors dyed in the smaller vats.
Before spun yarn can be dyed, it needs to be put into a reeled skein. This is basically a loose loop of yarn. It allows the dye to circulate throughout each strand of yarn. We hang reeled skeins on a rack inside a special caddy, which we then wheel in to the dye vat.
While we dye most of our colors over natural, off-white wool, we use a heathered gray base for some of our other colors. The heathered gray base is a blend of off-white with gray or brown created during the spinning process.
We formulate all of our own dye recipes here at the mill, and make our dyes with mixtures of primary and secondary colors in powdered form. We have a small sample machine that dyes tiny skeins of yarn for new color development and color testing.
Each batch of yarn requires between 40 and 400 gallons of water to dye. Not only do we use a huge amount of water, the water needs to be very pure and highly filtered. Luckily we are able to reuse 70-80% of our dye water thanks to our reverse osmosis filtration system. To learn more about our eco-friendly dyewater system, see our posts on How We Recycle our Dye Water and New Innovations in Dye Water Recycling.
Once we place the yarn in the dye vat, the machine runs though computer-controlled cycles. The process is similar to a washing machine. Each color requires a certain pH and temperature while the dye water circulates. Then a number of rinse cycles ensure the yarn is color fast.
Wool absorbs a huge amount of water (it can absorb 30% of its weight without even feeling wet!). As a result, the yarn must undergo several steps after it has been dyed to remove all the moisture.
First, the yarn goes into the extractor, which works like a large centrifuge. It’s a bit like the spin cycle in a washing machine.
Finally, a radio-frequency dryer dries the yarn. The radio frequency dryer uses radiation, sort of like a microwave. A conveyor belt slowly carries the yarn through the machine to remove all moisture. After this step, the yarn is all ready for us to package it into a skein, ball, or hank!
Like this post? Pin it!